Bearing Rings Automatic Forging Robot
Bearing Rings Automatic Forging Robot for One time heating+open/closed punch press+swing arm manipulator
The solution of using a
one-time heating automatic forging robot for bearing rings combined with an opening and closing punch press and a rocker arm manipulator is usually provided by professional automation equipment companies, such as Dongguan Fityou Robot Automation Co., Ltd. These companies can provide customized automatic forging production lines.
This automated forging production line usually includes multiple areas such as material preparation area, forming area, and sizing area. In the material preparation area, bar materials are stored on shelves and preheated through a heating furnace. Subsequently, the bar material is cut into appropriate lengths by a cutting press and may enter a secondary heating furnace for further heating.
In the forming area, the bearing ring material heated once will be sent to the opening and closing punch for forging. At this point, the rocker arm robotic arm (also known as the swing arm forging robotic arm) plays a crucial role in transferring materials from the heating furnace or cutting press to the press, and performing necessary transfer operations during the forging process, such as upsetting to forming, and then to the bottom cutting die. These robotic arms typically use a three-axis mechanism and are equipped with specialized high-temperature resistant gripper arms to grip products.
The rocker arm robotic arms provided by companies such as Dongguan Huike are not only suitable for the automation transformation of old equipment, but also for the needs of new automatic forging production lines. Based on the weight of the product and the forging process, customers can choose different models of robotic arms, such as single arm stepper beam forging robotic arms or double arm stepper beam forging robotic arms.
In addition, this automated forging production line also emphasizes safety and efficiency. For example, by setting multiple robotic arms of the same model on both sides of the first and second punch presses, it is possible to ensure that the product does not require manual intervention during the molding process, thereby achieving the goal of automatic molding. At the same time, advanced equipment such as forging presses with variable frequency speed regulation and electronic camshafts, as well as forming molds equipped with lower ejection mechanisms, can also improve production efficiency.
Overall, the solution of using a one-time heating automatic forging robot for bearing rings combined with an opening and closing punch press and a rocker arm manipulator is an important component of modern forging production. It can improve production efficiency, ensure worker safety, and reduce production costs.
1,Material and equipment information
1) Material: Less than 4.0KG (bar weight 1.4-4.0KG, material diameter 55-70mm).
2) Equipment: 400T closed punch press/250T open punch press.
Process Flow:
Elevator automatic material handling - material heating - temperature measurement and sorting -
400T punching
machine "upsetting+forming" -250T punching machine "cutting bottom"
Forging Process Flow
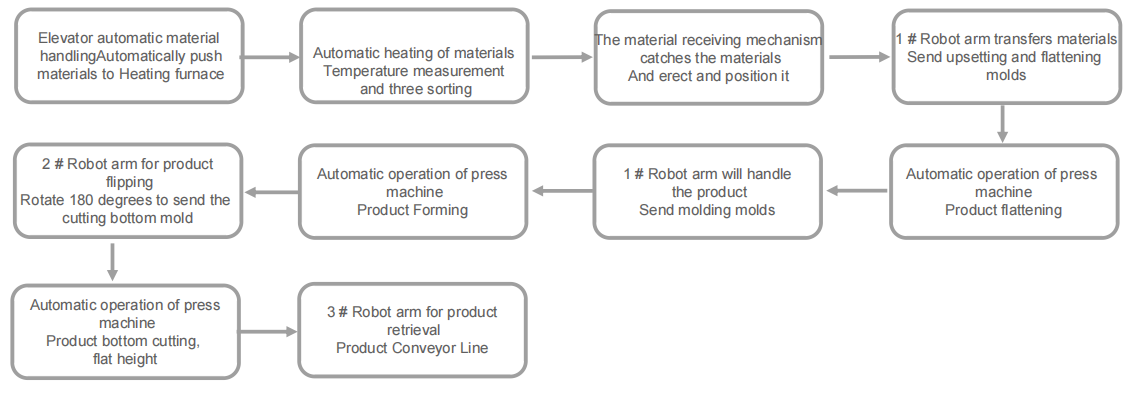